Episode 2
“Freeform Design”
by Hironao Kato (MagnaRecta)
ジオメトリカルな格子状のマネキンをご覧になったことはありますか?3Dプリンティングにさまざまなテクノロジーを統合(あるいはハック)してつくられ、A-POC ABLE ISSEY MIYAKEの店頭でも活躍しています。手がけているのはMagnaRecta(マグナレクタ)の加藤大直。この130(ワンサーティ)という名のまったく新しいブランドは、多くの機能や製造プロセスの優位性を備え、価値を循環する方法そのものでもあるようです。デザイナーの宮前義之とともに、その背景と可能性を語ります。
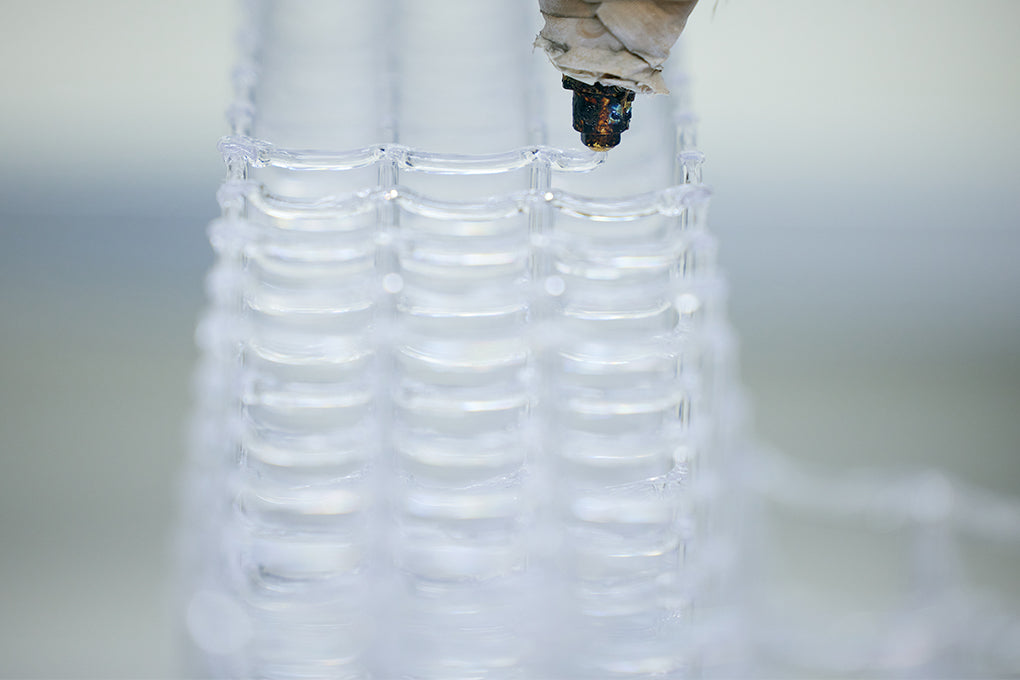
東京・日本橋。江戸の商人の街として栄えた名残は、奥行きのあるビルに問屋や倉庫がひしめく路地にいまもとどめています。MagnaRectaの拠点、つまりデザインのスタジオでありプロダクトを生み出すファクトリーも、そのような一角にありました。簡素なドアの内側に拡がるのは、もとは倉庫だったという天井が高く間仕切りのない空間。アルミのフレームで構成された大きな3Dプリンターが、ゆっくりと規則的に駆動しています。
ただし、その動き方はこれまでの3Dプリンターとはまったく異なるものでした。通常であれば下から上へ層を重ねるようにして立体物を造形していくはずなのに、MagnaRectaの「130」はタテとヨコ、あるいはナナメへと棒状にフィラメントが射出され、ジオメトリカルな格子状のプロダクトが生み出されていきます。
つまり面(二次元)や多面的な立体(三次元)ではなく、線(一次元)を組み合わせるというユニークなアイデア、または緻密な空中造形というイノベーション。3Dのプリンターとしてはあるいは本意ではないかもしれませんが、この構造によって軽量性と堅牢性を両立させ、製造にかかる時間と費用を圧縮し、工業製品のような精度と工芸品のような温もりを備えることを可能にしたのだと、MagnaRectaの創業者でCTOの加藤大直氏は語るのですが、まずはその背景から対話は始まっていきます。
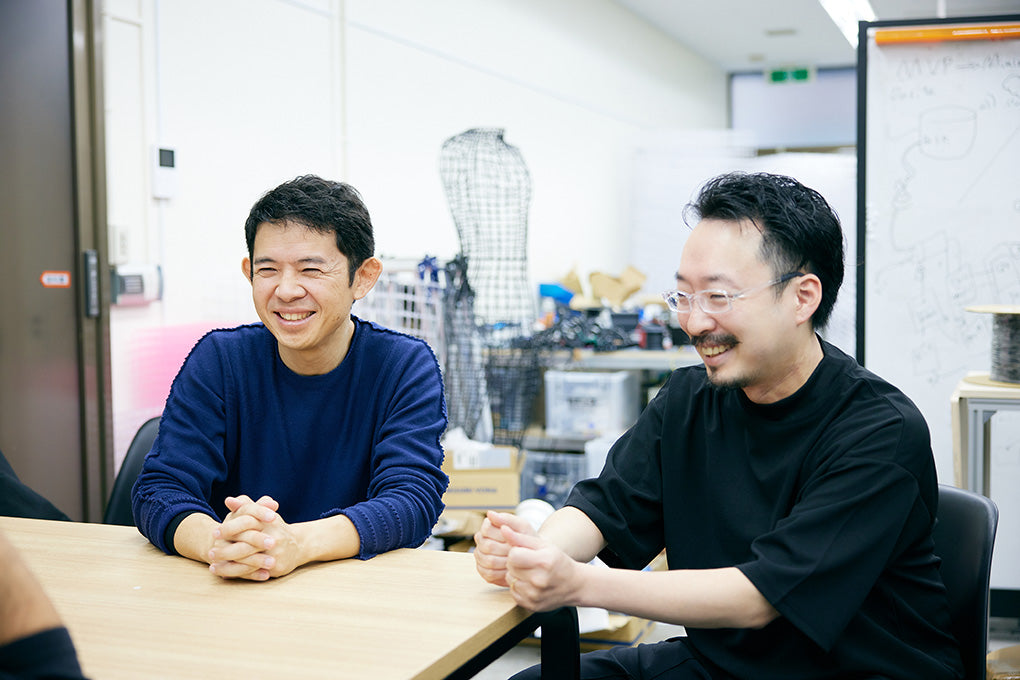
──130の開発にいたるまでには、A-POC ABLE ISSEY MIYAKE(以下、A-POC ABLE)との長いやりとりがあったそうですね。
加藤大直(以下、加藤) 遡ると2018年頃でしょうか。僕は当時、東京大学の川原(圭博)先生の研究室に関わっていて、あるプロジェクトに関わる論文、開発、実装のお手伝いをしていたんです。というのも、当時は友人の長谷川 愛さん(アーティスト/デザイナー)が研究員として所属していて、そのつながりがあったので。それである時、研究室のみんなとイッセイ ミヤケのオフィスへ遊びに行くことになり、僕もついていったんです。そこで初めて、宮前さんにお会いしました。
宮前義之(以下、宮前) そうでしたね。懐かしい。当時はまだISSEY MIYAKEのデザイナーでした。
加藤 ずいぶん大勢で押しかけたような記憶があります(笑)。いまは九州大学でご活躍されている、折紙工学の斉藤(一哉)先生などもいらっしゃって。蒸気で布が折られていく様子を見たり、先生が「これは何々折りですね」とその名称や仕組みを解説したり。とにかく面白かった。そのなかでも特に印象に残っているのが、イッセイ ミヤケのみなさんがとにかく手を動かしてつくっていたこと。泥臭いまでに。
いまでこそ3Dプリンターのようなエレクトロニクスを扱っていますけれど、もとは僕も美大(NYのパーソンズ美術大学)でプロダクトとインテリアを専攻していましたから、どちらかというとガチャガチャと手を動かす性分なんです。だからとても親近感を覚えたんですね。
──イッセイ ミヤケのものづくりに共鳴する部分があった?
加藤 そうです。11年に日本に帰国する前は、アメリカでプロダクトデザインの仕事をしていたのですが、当時のあちら側のものづくりは、長く使ってもらうことを前提とせずに、ポンポンとつくっていくようなテンポラリーなところがありました。建築などもそうですが、プロダクトデザインも価値が長く続くことが大切だし、大学でもそれを学んでいたはずなのに、ビジネスになると相反しているように感じたんです。
僕はどうしてもその部分が腑に落ちなくて、就労ビザを取得してデザイナーとして働いていたんですが、日本に帰ってきた。そういう背景があったので、イッセイ ミヤケの仕事場の雰囲気により強く共感したのかもしれません。
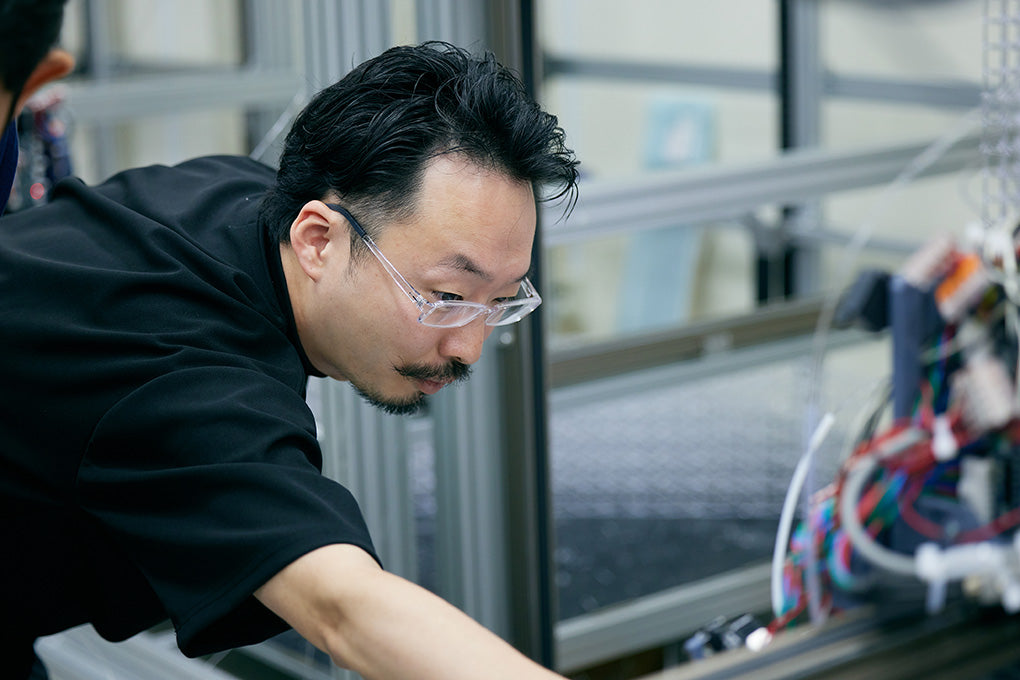
──そのようななかで、3Dプリンティングとはどのように関わっていたのですか?
加藤 最初は趣味というか、それを使って遊んでいました。アメリカにいた頃からそのような感じで、帰国してからしばらくして3Dプリンターでオープンソースのコミュニティ(RepRapコミュニティジャパン)を立ち上げて展示会への出展などを行っているいうちに、「3Dプリンターをオープンソースで日本に持って帰ってきた男」のように見なされてしまい(笑)、やむなく起業しました。
──それが「MagnaRecta」の前身である「Genkei」ですね。
加藤 はい。3Dプリンターの企画、開発、販売を行なっていました。プロダクトデザインを飛び越えて、電気工学やロボティクス、デジタルファブリケーションを突き進むことになりました。けれどまったくの門外漢だったかといえば、そうではなかったんです。大学で専攻していたのはプロダクトデザインですが、どちらかというとコンセプトデザインの領域にも近くて。例えばモーターショーに出展されるようなコンセプトカーとか、『ブレードランナー』のような映画のプロダクションデザインとかが研究の対象でした。
一方で僕の個人的な理念としては、そういった未来を示すようなコンセプトを映画や展示会などで発表するだけではなく、「どうやったら社会に実装できるか」を追求したいというものがあった。なので3Dプリンターという、アイデアをダイレクトに出力する可能性をもった新しい技術との相性が、とてもよかったんだと思います。
──そして2018年に「MagnaRecta」へと組織変更されました。
加藤 当時はデジタルファブリケーションがブームのようになっていて、僕たちがつくる3Dプリンターも多くの顧客を獲得できていました。けれど先ほどお話ししたように、もともと目指していたのは新しいコンセプトを社会に実装していくこと。なのでその目標に向かってビジネスの方針も組織も一新したんです。ようは3Dプリンター屋さんから、改めてデザインの道に戻っていくということ。宮前さんとお会いしたのは、ちょうどその転換期でした。
宮前 オフィスもまだここではなくて、赤羽橋のほうでしたね。3Dプリンティングという新しいテクノロジーにはもちろん注目していましたし、加藤さんが目指されていることにもとても興味がありました。
加藤 僕もイッセイ ミヤケで拝見した仕事場の風景に異様にシンパシーを感じました。つくっている服や布はジオメトリックだったりするのに、それをとんでもなく緻密に手を動かしながら生み出している。それがすごく素晴らしいと思ったんです。
僕たちの会社としても学ぶことは多かったし、ファッションというフィールドで何かできたらという野心もありました。とはいえ具体的に何かを一緒につくりましょう、といきなり始まったわけではなかったですね。基本的にはキープコンタクト。いまみたいに宮前さんたちと会話をしながら、共同研究というか、新しい可能性を探っていきました。
宮前 それで当時の僕たちの課題について話しているときに、マネキンのことが話題になりました。それまで僕たちが使っていたものは樹脂製の量産品ですが、オリジナルをつくろうとすると、金型からつくる必要があった。理想としては衣服に合わせていろいろな形が欲しいのだけれど、オリジナルのマネキンでそれを叶えようとすると、とてもコストがかかります。
そういうなかで、もし3Dプリンターでつくれるようになれば、新しいソリューションになるかもしれないと思ったんです。素材や形状などすべてまっさらな状態から話していきました。
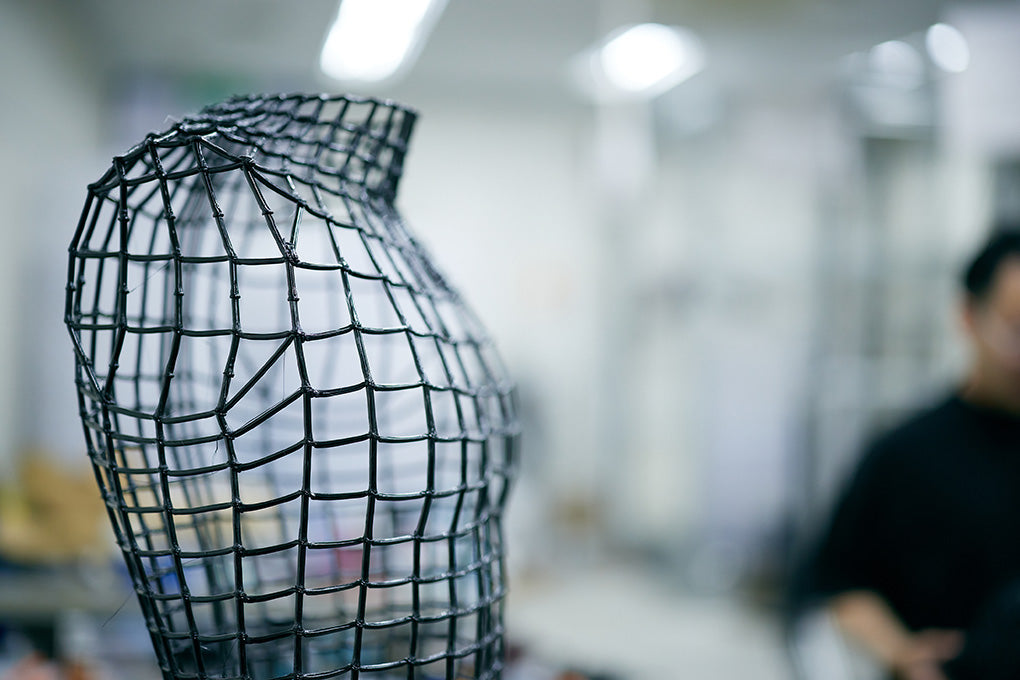
──3Dプリンターでつくったマネキンという先行事例はあったのでしょうか?
加藤 量産を前提にしたものはないですね。あまりにもニッチすぎたのかもしれません。彫像のような造作物はもちろんあったかもしれませんが、商用のマネキンは存在していませんでした。
宮前 本当にいろいろとトライ・アンド・エラーをしてきましたよね。素材の検証から始まりましたから。いまはA-POC ABLEの店頭で使わせていただいていますが、ここにいたるまでに何段階もの進化を経ています。一番最初のマネキンは「TADANORI YOKOO ISSEY MIYAKE 0」(19年)のお披露目のもの。A-POC ABLEがいまにいたる前身となったプロジェクトです。東京・代官山のT-SITEのギャラリーで展示したのですが、とても反響をいただきました。
一代目はアフロやリーゼントなどの多様なヘアスタイルのマネキンが誕生して、三代目あたりでは歌舞伎の見栄を切ったポーズのマネキンが登場しました。これは実際に歌舞伎役者の方にポージングをしていただき、それを3Dスキャンしています。iPhoneの3Dスキャンでひたすら写真を撮りましたよね。
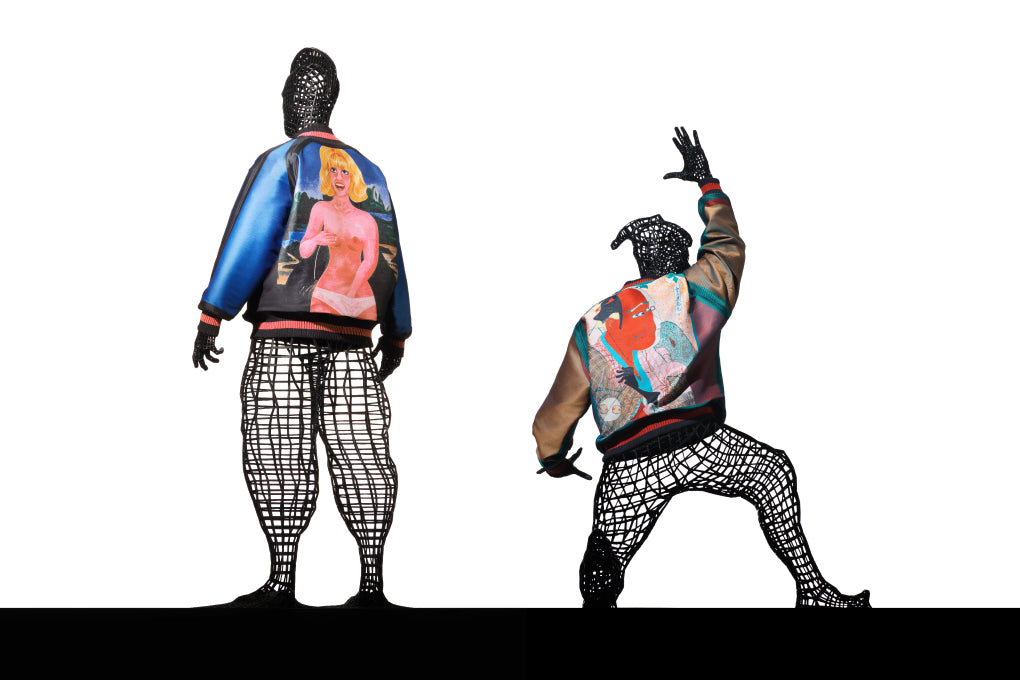
加藤 そうでしたね(笑)。お分かりかと思いますが、新しいもの大好きで。当時出始めたばかりのフォトグラメトリ(※)を用いたんです。マネキンの構造としては、首だけ取り外せるようになっていたり、メッシュ状になっていたりといまにつながるものでしたが、このときはまだ従来と同じ積層型でした。
※写真測量。複数枚の写真から3Dモデルを作成する技術
宮前 マネキンとしては独創性があり革新的だったと思います。積層の造形であったとしても、この展示では問題はなかったのですが、店頭での実用化を考えると課題が残りました。例えば製造のスピードを上げて出力しようとすると、滑らかさに欠けてしまい、細かな凹凸が服に引っかかってしまう。手作業で後処理をすれば問題ありませんが、時間とコストを要してしまいます。
店舗でマネキンとして実装していくには、この点をクリアする必要がありました。逆に言えば、それさえ解消できれば実用化の目処が立ちます。2021年にA-POC ABLEがブランドとして始動するにあたって加藤さんとの共同研究は進んでいき、いまの方法につながる提案をいただきました。
加藤 大きな転換でした。同じメッシュの構造ですが、はっきり言うと、もう3次元のプリントではなくなったということです。積層痕というのが3Dプリンターの弱みであることは、ずっと認識していましたし、割れやすさや荷重の弱さ、それに伴って大きなサイズのものを出力できない、という問題もついてまわりました。展示用としては要件は満たせても、布をまとわせるものとして常用するには不十分でした。
けれど解決策はなかなか見つかりません。2、3年は悶々としていたと思います。当時の時代背景としても、3Dプリンターは商業利用しにくいよね、というムードが物理的な理由とともに形成されつつあって。論文を読んだりしながら新しい方法を研究していました。そのようななかで「空中造形」と出合いました。論文としてはかなり昔から出ていたし、おもちゃの3Dペンもその一種ですが、決して新しいわけではありません。実際、その考え方だけではどうにもならなかったんですが、光明はあるかもしれないと感じました。それで宮前さんに見てもらったんです。
宮前 鳥かごのようなプロトタイプを見せていただきましたよね。それまでの積層のものとは違って、ツルツルしていました。これなら布も引っかからないし、実用化できるかもしれないと思いました。
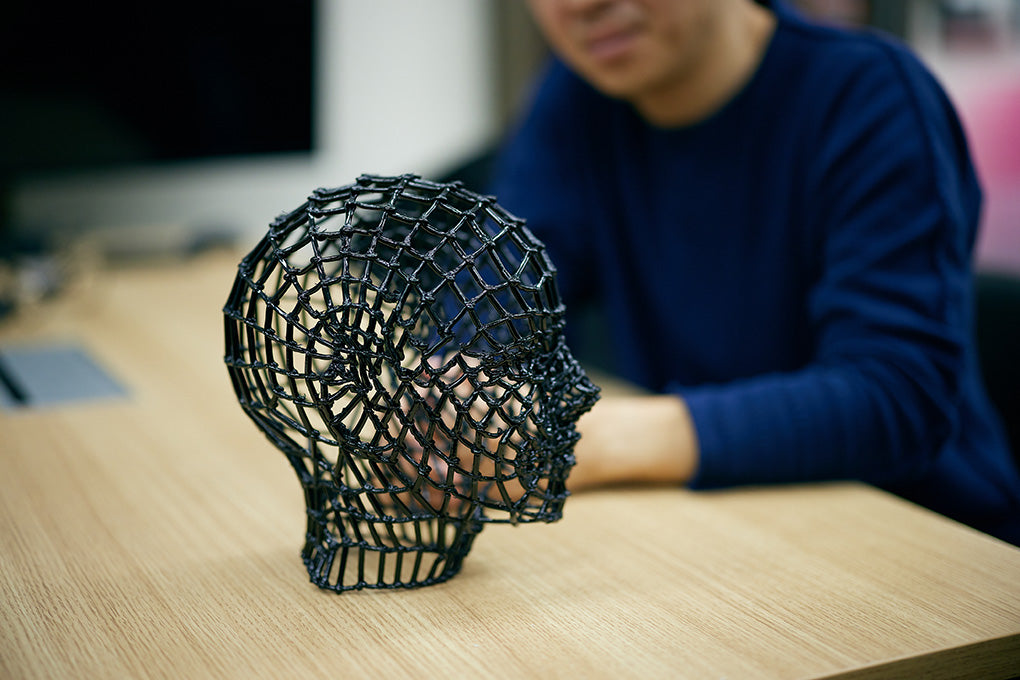
──つまりそれが層を重ねるのではなく、棒のように射出するといういまの方法につながった。
加藤 そうです。ただ棒のように樹脂を射出しても、造形は難しいし強度も足りません。けれど棒と棒が重なれば強くなる。単純な話ですが。3Dプリンターはかつてもいまも、二次元の積層です。層を重ねていく限りザラザラしてしまう。けれど僕らが開発した方法は一次元なんです。棒で立てていく。つまり、そういう意味で三次元のプリントではなくなりました。
──構造は一次元で、プロダクトとしては三次元。3Dプリンターの使い方を根本から変えてしまいました。
加藤 この方法を追求していったときに、デザインの視点から突き詰めて考えたことがあります。これは一体どういうものなのか。わかったのは、僕らは既存の3Dプリンターの技術や価値観とは、真反対のことをやっていたということです。二次元ではなくて一次元で射出して、重く堅牢なものではなくて、軽量でスピーディにつくることを目指していたんです。
宮前 時間という視点はとても大事だと思いました。実装のコストに直結しますから。例えば展示のみの作品をつくるのなら、コストや時間をとことんかけてもいいかもしれませんが、僕たちが加藤さんと目指していたのは店頭でマネキンとして実際に使えるものだし、それはつまり既存のものとのコストの比較になってきます。
その点でいうと、どれくらい製造の時間を要するかがコストに直結します。そして軽さというのも輸送に関わってくる。加藤さんからこの新しい3Dプリンターの造形技術を教えていただいたときに、僕たちがこれからのマネキンに期待すべき条件や設定が、よりクリアになっていったんです。

──格子状の構造のメリットはほかにもありますか?
加藤 3Dプリンターは射出がうまくいかないことがあるのですが、これまでの方法だとスパゲッティのようになったり、面が割れてしまったりする。そうなると最初からやり直しが必要になることもあります。もちろん130でもうまくいかないことがあるのですが、僕たちとしてはOKです。なぜかというと、失敗した部分だけを切りとって、新たに射出した棒状のフィラメントでつないでいくことができるから。いわゆる造形失敗が生じない構造であるともいえます。
──面的な構造がなく一定の規則性があるからこそ、やり直しも簡単にできる。
加藤 そうですね。この優位性は製造の過程においてだけでなく、プロダクトの完成後にも生きてきます。修理や補修や何か新しいものを付加することも簡単に行なうことができるので。どれほど丈夫につくったとしても、使っていれば部分的に壊れてしまうことがあるかもしれませんが、130ならすぐに元通りにすることができます。
僕たちがものづくりをする上で達成したいのは、ものの価値を失うことなく、できるだけ長く使っていただくことです。「骨折」と僕たちは言っているんですが、どこかが折れてしまっても陶磁器の金継ぎのように直すことができるし、気に入らない部分を取り外したり、何か新しい機能を付加することもできます。
宮前 とても共感できます。これまでのマネキンも修理するのは簡単ではなかったですから。部分的に壊れているだけでも、一体ごと使えなくなってしまうことだってありました。けれど130にはものづくりの柔軟性があって、価値を継いでいくことができる。
加藤 「継美変容」という造語をあてているんですが、僕たちのものづくりの根幹には、美を継ぎ、形相は変容していくという哲学があります。パーツは一本のPETの棒ですが、いかにして機能やつくり手の思い入れといった価値を持続させ、変容させていけるかを大切にしています。

──素材は既存のものですか?
加藤 はい。PETです。タテ3マス×ヨコ3マス×高さ3マスで大人のひとりの人の荷重に耐えられるほどの強さもあります。しかも100%PETの単一素材なので、リサイクルも簡単です。
──ソフトウェアやアプリケーションも従来のものを利用しているのでしょうか?
加藤 ベースの部分はいわゆる3DCGアニメーションなどで使うようなアプリケーションですね。そこに新しいプログラムをつくって拡張したり、ちょっとしたソフトウェアを加えたりしています。タテが先か、ヨコが先かなど、棒を射出していく順序を指示する段階では、手作業も必要だったのですが、それを自動化するアルゴリズムも開発しました。
宮前 すごい。その部分が自動化できてしまえば、ますます製造のスピードが加速します。ジオメトリカルな構造というプロダクトの見た目は変わらなくても、その背後のプロセスに革新がある。こういうお話を聞くと、とてもワクワクします。
加藤 僕らがかつて3Dプリンターの製造販売をしていた頃、特許をいくつかもっていたのですが、すぐに模倣されてしまったり、異なる機構で転用されたりしていました。ですから3Dプリンターの製造や技術でビジネスをするのではなく、それらを統合したソリューションによるビジネスにしたいと考えたんです。これまであまり知られていなかったのは、すべて水面下で開発をしてきたからですね。
あるいは見た目がそっくりなものはできるかもしれませんし、これまでも建材などの領域では似たような実験もされていたり、論文も公開されたりしています。しかしあくまで建材でコンクリートの骨組みの素材のようなものだったりすることが多い。それ自体がプロダクトとなるような研究や開発は、これまで一切されてきていなかったんです。3Dプリンターもアプリケーションやアルゴリズムも、単体で使っても意味がないものばかりで、7〜8つのオリジナルの要素技術を統合したオペレーションになっています。つまり同じような機能や造形の美しさをもったプロダクトをつくるのは決して簡単ではないと思います。
──美しさという点ではどのようなポイントを重視していますか?
加藤 形状やモチーフによって格子の粗密や棒の太さを調整しています。例えばマネキンでもボディに比べて頭や顔の部分は、密度は高くなっていて棒も細くしています。そのほうが表情などの細かな造形に適しているためです。必要があれば曲線の形状も射出できますね。
デザイナーとして気に入っているポイントのひとつに、棒状の樹脂の一本ずつが、ガラス細工のような質感を感じさせてくれるところも挙げられます。遠目からはジオメトリカルで無機質なプロダクトに感じますが、近づいて見てみると、うねうねと少し揺らいでいるような工芸的な質感があるんです。
宮前 棒が接合している部分も有機的な雰囲気がありますよね。透明なフィラメントを使ったプロダクトは特に、光が乱反射してとても綺麗です。
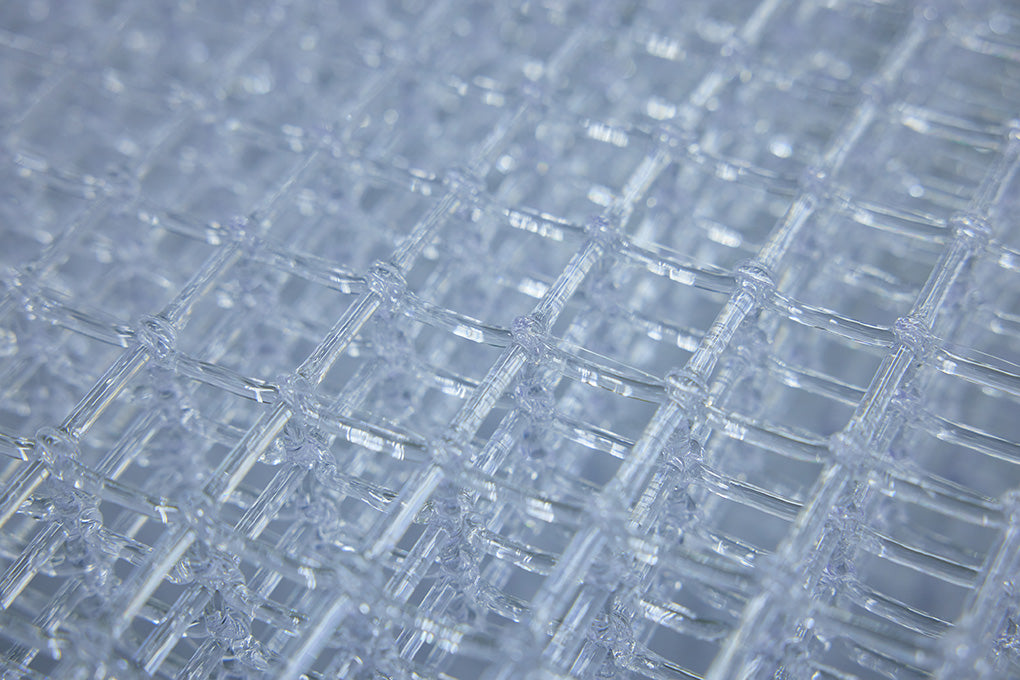
──先ほど、リサイクルというお話がありましたが、この点でも優位性がありますか?
加藤 はい。まずは単一の素材で構成されていること。そして軽量で壊しやすくもある。昔から使われている木の板ですら破砕するのはとても大変だし、リサイクルも難しい。工場で大きな機械を使わないと不可能です。一方で130はその部分も身軽です。僕らは麻袋の中に入れて叩いていますが、持ち運びがとても容易だし、それだけで再素材化のコストを圧縮することができます。
宮前 この部分もとてもすごいと思います。小さく循環させていく仕組みが現実のものになりますから。例えば店頭で使っていたマネキンを新しいポーズに変えようとなれば、これまでは破棄するしかありませんでした。けれど130なら古いものをお店のバックヤードで砕き、店舗間をつなぐ配送車に乗せて回収し、再素材化することができる。こういった仕組みを加藤さんたちと構築していきたいと考えています。
加藤 つまりこれは世界最小径のプロダクトサイクルにつながっていく。リサイクルという言葉はしばしば耳にしますが、ほとんどの商品は多様な素材で構成されていて、回収や分解の作業に多くの労力が必要になります。さらに分解した後にも、それぞれの専門的な再素材化の技術をもつ業者に分配したり配送したりしなければなりません。これによってどんどんコストがかさんでいきます。
けれど僕たちは自分たちで回収することができ、PETのリサイクル工場やあるいは僕ら自身でも再素材化することも可能です。製造、製品、回収、再製造という循環を、とても小さなループで行なっていきます。当然、ループが小さければ小さいほど、環境やコストの負荷が小さくなっていきます。なんというか究極の自作自演のようでもありますね。
宮前 理想的でもあり、最も現実的でもある。ものづくりのとても小さなサーキュレーションが生まれていくはずです。
HIRONAO KATO
加藤大直 MagnaRecta 創業者/CTO。1984年生まれ。米国・NYのパーソンズ美術大学卒業後、デザイナーとしてMckay Architecture/Design、Berm Design NYに勤務。2011年に帰国後、RepRap Community Japanを共同創設し、国内初の3Dプリンタ「atom」を開発、オープンソース化し、3Dプリンターの開発・製造・販売を行なうGENKEIを共同創業した。17年3月よりMagnaRectaに組織変更し、それまでに培ってきた3Dプリンターやロボティクスを活用したデジタルファブリケーションのハードウェア、ソフトウェアなどの産業ソリューションとデザインの両軸で提供している。24年、棒状のフレームを次々に繋げて立体構築していく革新的な立体造形技術をコアに持つブランド、130をローンチした。
次回のEpisode 3では“Protein Revolution #1”についてお届けします